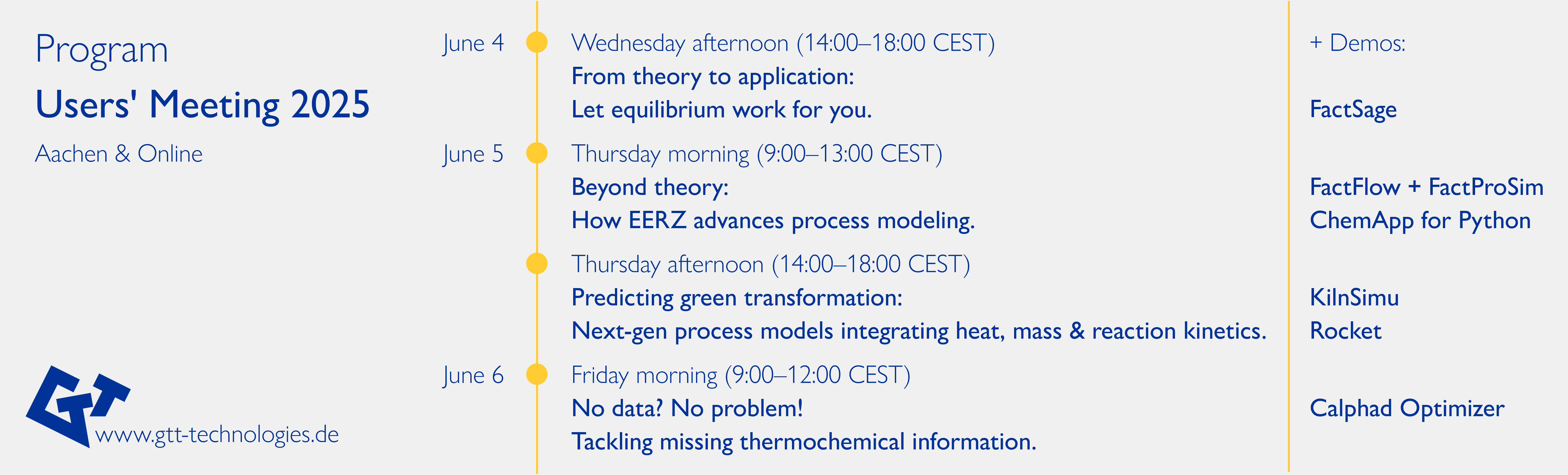
Users’ Meeting 2025: A hybrid event in Aachen.
Our 27th Users’ Meeting will take place from June 4 to 6, 2025 as a hybrid event in the heart of Aachen‘s old town.
On-site attendees will enjoy demos, networking, and a social program.
Online attendees will benefit from hybrid streaming for an engaging experience.
For all practical details such as venue access, arrival, lunch and dinner options, please visit our dedicated page: On-site Info.
Quick navigation
In memory of Abdulmonem Obaied
The 2025 Users’ Meeting will be dedicated to the memory of our colleague and friend Abdulmonem Obaied, who unexpectedly passed away this year. Abdulmonem was not only a brilliant scientist and valued team member, but also a warm person whose generosity and dedication touched everyone who knew him.
Please find the full tribute to Abdulmonem, honoring his life, work, and character, here.
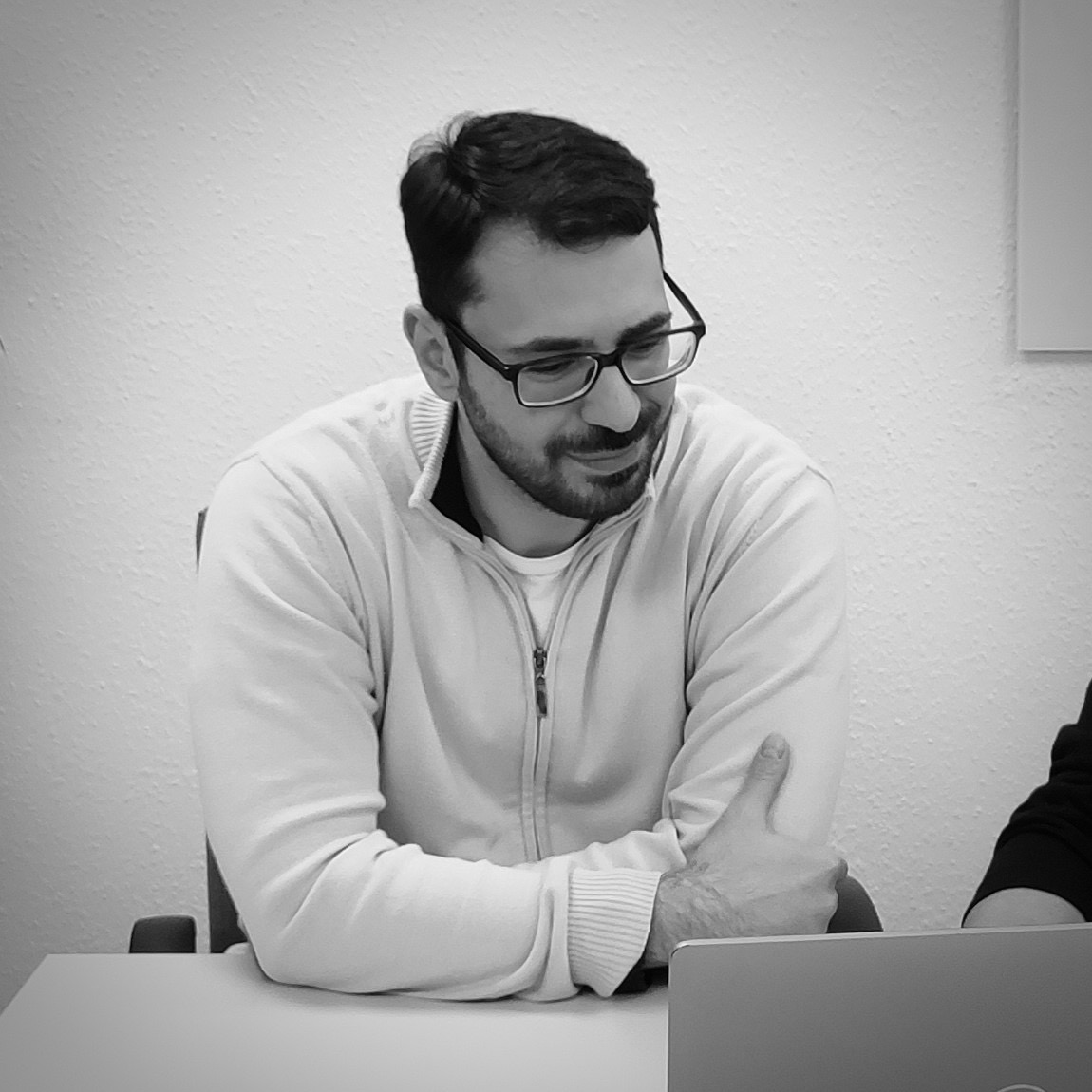
PROGRAM & SPEAKER
For directions, venue access, and meal options, please visit our On-site Info page.
Wednesday afternoon (June 4, 14:00-18:00 CEST)
From theory to application: Let equilibrium work for you.
Welcome & Introduction
Moritz to Baben (GTT-Technologies)
Stephan Petersen (GTT-Technologies)
Exergy calculations for systems exhibiting solution phases as well as compounds
Klaus Hack und Markus Reuter
Extractive metallurgists unmix complex mixtures arising either from ores and minerals or designed products and their functional materials to create high quality metals, compounds and alloys. To fully understand economic aspects of this endeavor, a deep understanding of solution chemistry is required be it solid solutions, high temperature liquid or aqueous solutions. Especially the configurational and excess entropies of a solid and liquid solution are important in this regard. For this reason, the simplified definition for calculating the exergy of non-ideal solutions as defined by Szargut is shown in this paper to be problematic. We reinterpret the equation Ex=(H-H°)-T°(S-S°), which is generally applied for the calculation of chemical and physical exergies of pure substances in the framework of solution phase thermodynamics. Here it is demonstrated that it is more rigorous to use full solution chemistry for deriving the enthalpies (H and H°) and entropies (S and S°) for a particular system of given composition. The suggested approach links H, H°, S and S° rigorously, which is not necessarily the case in the Szargut methodology. Using the case of a Fayalite slag it will be shown that using the Szargut approach leads to inconsistent results while the general Ex-equation provides a smooth transition from cases with solution phases to those exhibiting only stoichiometric compounds.
In the publication “Expanding the exergy calculation methodology of materials to include equilibrium calculations of complex systems” which is in print now in Journal of Sustainable Materials two case studies are given for elemental metallic systems while two further studies cover systems with oxidic components, among these the one demonstrated in the presentation.
Klaus Hack (GTT-Technologies)
Use of FactSage for the production of supplementary cementitious materials from slags and tailings
Michiel Giels and Mathijs Schuurmans
Concrete is the world’s most widely used material after water, yet its key component, Portland cement, accounts for approximately 7–8% of global anthropogenic CO₂ emissions, primarily due to limestone calcination. Reducing the cement industry’s carbon footprint hinges on substituting Portland clinker with supplementary cementitious materials (SCMs). However, the availability of traditional SCMs is decreasing as other industries decarbonize, leading to higher prices and limited supply. Despite growing interest in alternative SCMs from industrial residues or raw materials, their development remains largely based on trial and error. While computational tools like statistical modeling offer support, the reality is that SCMs cannot yet be designed from first principles alone. In this presentation, we showcase research at KU Leuven on predicting the mineralogical composition and reactivity of SCMs using thermodynamic software (FactSage). We present two case studies illustrating the production of reactive SCMs from bauxite residue and electric arc furnace (EAF) slags, leveraging neural networks. Finally, we outline our next steps toward developing an advanced SCM production model and invite discussion and input to further refine this approach.
Michiel Giels (KU Leuven)
Fission product speciation under nuclear reactor operating conditions
M. Rochedy1, V. Klosek1, F. Cornier1, C. Onofri-Marroncle1, D. Drouan1, D. Reyes2, M. Cabié3, J. Lechelle1, C.Riglet-Martial1
1 CEA, DES, IRESNE, DEC, Cadarache, Saint-Paul-Lez-Durance, 13108, France
2 CIME, École Polytechnique Fédérale de Lausanne (EPFL), Lausanne, Switzerland
3 CP2M, Université Aix-Marseille, 13013 Marseille, France
During reactor operation, the fuel, composed of uranium oxide, undergoes numerous transformations, including the fission of fissile nuclei, leading to the generation of a wide variety of fission products (FPs). These FPs can be classified into different categories: fission gases and other volatile fission products (e.g., Xe, I, Cs), metallic precipitates (e.g., Mo, Ru), oxide precipitates (e.g., Cs, Ba), and those dissolved in the UO₂ matrix (e.g., Sr, Zr). Identifying the possible interactions between the UO₂ matrix and the various fission products (FPs) allows us to better predict and understand their behaviour under both normal operating conditions and accidental scenarii. In this context, iodine and caesium are in particular studied for Stress Corrosion Cracking induced by Iodine (CSC-I) which can occur during a power ramp. , and their release under accidental conditions due to their radiotoxicity. The use of chemical thermodynamics software is therefore essential to predict the speciation of these FPs. This presentation will focus on two examples of work being carried out in the laboratory on these subjects. The first focuses on the speciation of I in the UO2 matrix and the second on the speciation of Cs in the presence of aluminosillicate in a UO2 matrix.
Morgane Rochedy (CEA IRESNE)
A path towards semantically correct and information rich databases
F. Tang1,, B. Bocklund2, R. Otis3, M. to Baben1, J. Zietsman4
1 GTT-Technologies GmbH, Herzogenrath, Germany
2 Lawrence Livermore National Laboratory, Livermore, CA, United States
3 Proteus Space, United States
4 Ex Mente (Pty) Ltd., Gauteng, South Africa
Computational thermodynamics faces a pivotal challenge in database management, which is becoming even more obvious as we transition from established manual workflows to the emerging machine-learning era with high throughput processing. Traditional approaches to thermodynamic data handling often suffer from validation inconsistencies, poor structuring, insufficient metadata, limited extensibility, and difficult string interpretation mechanisms. Ultimately, these points lead to Calphad databases failing the “Interoperability” and “Reusability” criteria of the FAIR data principles.
In this work, we present ThermML, a novel XML-based format designed to supersede TDB databases by combining human-readable elements with robust machine-processable thermodynamic data structures. By implementing strict validation rules and rich metadata capabilities, ThermML simultaneously improves data quality and computational accessibility for modern Calphad applications. The new format addresses the fundamental limitations of current database designs by implementing five core principles: rigorous data validation, consistent structural organization, rich metadata integration, extensible architecture, by conceptually surfacing domain specific implicitness, while implementing all cornerstones of FAIR data.
ThermML offers several key advantages over existing formats. First, its schema provides immediate validation during development, allowing researchers to identify errors before computation begins. Second, the hierarchical XML structure naturally maps to thermodynamic models, making relationships between parameters explicit. Third, the format supports comprehensive metadata annotation, essential for both traditional and advanced research data management, a requirement in many global research initiatives. Fourth, the extensible design accommodates new model types, model parameters and attributes and parameters without breaking backward compatibility. Finally, by moving away from string-based data representation, ThermML eliminates a significant source of errors in thermodynamic calculations stemming from hard to detect input errors.
The implementation currently exists as a community driven open development project accessible under https://github.com/flotang-gtt/ThermML. Experimental support using ChemApp is shown, with integration into both pycalphad and FactSage Calphad Optimizer planned. We will demonstrate significant improvements in workflow efficiency, with researchers spending less time debugging data inconsistencies and more time on thermodynamic analysis. Examples of this will be shown using modern IDEs that showcase its practical benefits, including immediately accessible documentation, intelligent autocompletion of modeling parameters, and on-the-input validation. These features make ThermML particularly accessible to new researchers while providing experienced Calphadians with powerful tools to manage large and complex datasets.
We invite you to take part in the discussions and on the associated git repository where the XML Schema is iterated and documented: https://github.com/flotang-gtt/ThermML
Florian Tang (GTT-Technologies)
Effects of Fe/Al on P compounds in municipal sewage sludge derived biochars and impacts of adding K compounds
Naeimeh Vali (University of Borås)
Uncovering one of the last unknowns in the steel industry, i.e., slag carryover through FactSage simulations
Ashok Kamaraj1 #, Gopi K Mandal2, Gour G Roy3
1 Department of Materials Science and Metallurgical Engineering, Indian Institute of Technology Hyderabad, (IITH), Kandi, Sangareddy, 502285, India
2 CSIR-National Metallurgical Laboratory (CSIR-NML), Jamshedpur, India
3 Indian Institute of Technology (IIT), Kharagpur, India
Carryover of oxidizing slag from the primary steelmaking furnace during tapping affects the quality of the liquid steel in several ways. Secondary steelmaking practices, such as deoxidation, desulphurization, vacuum degassing, as well as inclusion control in the liquid steel bath, are greatly influenced by the amount and characteristics of carryover slag. Thus, control and minimization of carryover slag during tapping is essential by suitably modifying the operational practice.
The amount of slag carryover (SCO) during the liquid steel tapping from the basic oxygen furnace (BOF) process has been estimated using a thermodynamic model that ensures the matching of the predicted bath silicon with that of experimentally measured silicon in the ladle furnace. FactSage 6.4 has been used for thermodynamic analysis. A simple correlation has also been established to estimate SCO immediately after the tapping process using the readily available plant data. Viscosity, interfacial tension of the slag, impurities in the liquid steel, and the tapping temperature have been found to have a profound effect on the amount of slag carryover. Further, water model experiments conducted with water and different types of oils (coconut oil, petroleum ether, and mustard oil) to study the influence of physical properties on the carryover of overlying liquid during the tapping process are compared with the FactSage findings. It has been observed that the FactSage predictions are in good agreement with the water model results.
The advantage of the present method of SCO estimation compared to the other methods and the industrially viable control measures for minimizing SCO is discussed in light of clean steel practices. Further, industry trials have been conducted to validate the control of SCO by tuning the BOF slag properties.
Ashok Kamaraj (Indian Institute of Technology Hyderabad)
Introducing FactSage 8.4 – From Equilib to FactFlow, FactProSim & ChemApp for Python
Moritz to Baben (GTT-Technologies)
End of day
Thursday morning (June 5, 9:00-13:00 CEST)
Beyond theory: How EERZ advances process modeling.
Introducing FactFlow – Flowsheeting made easy
Shivani Gonde (GTT-Technologies)
Moritz to Baben (GTT-Technologies)
Introducing FactProSim – EERZ made easy
Ömer Büyükuslu (GTT-Technologies)
Shivani Gonde (GTT-Technologies)
ChemApp for Python – Exploring the chemical space
Bruno Reis (GTT-Technologies)
Ömer Büyükuslu (GTT-Technologies)
Exploring thermochemical effects of hydrogen in blister copper deoxidation with ChemApp for Python and machine learning optimization
Alberto Rivera Romero
CENIM-CSIC
High-purity copper, valued for its excellent conductivity, is essential for the energy and digital transitions. In conventional blister copper deoxidation, methane bubbling effectively reduces the dissolved oxygen content to below 0.15 wt.%. However, this method results in the generation of carbon dioxide (CO₂) and has a relatively low average efficiency of 30 %. Replacing methane with hydrogen emerges as a promising approach to simultaneously lower CO₂ emissions while enhancing the reduction performance. The success of such hydrogen-based copper metallurgy requires detailed thermodynamic insight into the Cu-O-S system, including the presence of multiple minor impurities (As, Ni, Pb, Ag, Sb, etc…).
This study employs FactSage 8.3 and ChemApp for Python to perform a systematic, comparative thermodynamic evaluation of Cu–S–O melt deoxidation by methane versus pure hydrogen. The deoxidation dependence on temperature, oxygen, and sulfur contents, as well as minor impurity levels, are analyzed. Industrial conditions were simulated including the thermodynamics of oxygen–fuel flame products and their interactions with liquid copper for methane burners, quantifying reductant species at the surface and their interactions with the liquid copper surface.
Results demonstrate that hydrogen bubbling delivers superior deoxidation across a wider gas temperature range, as hydrogen reacts directly with dissolved oxygen, while methane first undergoes an endothermic thermal decomposition. Impurity identity and concentration are identified as critical factors controlling oxygen activity and overall reduction efficiency. In combustion analysis, the oxygentofuel ratio governs flame temperature and reductantspecies fraction. Adiabatic oxygen–methane flames show a higher proportion of reductant species compared to oxygen–hydrogen flames in most of the O2/gas ratios. However, the adiabatic flame temperature is higher in oxygen-hydrogen flames. The reductive behavior at the copper interface is comparable, slightly higher in the case of methane.
The results of this study enhance our understanding of molten metals refining using 100 % hydrogen bubbling and combustion, which will aid the advancement of more sustainable and efficient metallurgical processes.
Alberto Rivera Romero (CENIM-CSIC)
How ChemApp for Python is used to simulate Me2H₂: Storage and transport of H₂ using redox reactions
M. Sc. Ahmed Mansy
TU Clausthal, Institut für Metallurgie, Clausthal-Zellerfeld 38678, Germany
Hydrogen is expected to be crucial for future industrial decarbonization. However, hydrogen’s low density and high required liquefaction energy pose significant technical and economic barriers to transport and storage. Instead of transporting hydrogen bound in liquid ammonia, or via liquid organic hydrogen carriers (LOHCs), a promising alternative is storing energy in high-density “precursors”. Specially designed iron-based systems, such as those used historically in the steam-iron process, are being reconsidered for this purpose. The project 𝑀𝑒2𝐻2 focuses on identifying suitable material systems and developing the associated process and plant technology to create a solution that will be able to transport and store large amounts of hydrogen efficiently.
The present work demonstrates the use of ChemApp for Python to develop a modern and efficient steam-iron process. The envisaged process is divided into a finite number of localized equilibrium reactors which are linked by streams into a flowsheeting network representing the complete process stages. This corresponds to the primary modeling paradigm of applying ChemApp. By extension into a versatile tool via reusable Python components, it is possible to construct and develop such a complex process with several operational units.
The developed thermodynamical process model aims to maximize efficiency by considering all process steps (reduction/oxidation) and the associated phases, temperatures, and pressures in the reactors. For the endothermic reduction step, the necessary process heat can efficiently be supplied via partial oxidation of hydrogen with oxygen. ChemApp is therefore combined with numerical algorithms to find the optimal procedures to achieve this. Additionally, the model incorporates techniques for heat recovery, such as utilizing the heat energy in the top gas. This is done by integrating heat exchangers and compressors as operational units, which are also modelled with ChemApp. Furthermore, steam generation for the oxidation process is modelled and incorporated into the overall energy management strategy.
Ahmed Mansy (TU Clausthal, Institut für Metallurgie)
Thursday afternoon (June 5, 14:00-18:00 CEST)
Predicting green transformation: Next-gen process models integrating heat, mass & reaction kinetics.
Simulation of open bath furnace process for hot metal production with ChemApp for Python
The decarbonization of the iron and steel industry demands the replacement of the blast furnace process with lower CO2-emitting technologies. One feasible technology is dividing the blast furnace process into two distinct process steps: The direct reduction of the iron ore and melting of the directly reduced ore. One suitable furnace for the second process step is known as the Open Bath Furnace (OBF) or Electric Smelting Furnace (ESF). To better understand this melting process a thermochemical simulation was set up based on the effective equilibrium reaction zone approach: The OBF was divided into several reaction zones and coupled with kinetic parameters and recursive mass streams. The simulation was carried out using ChemApp for Python with coupled FactSage databases and data from published literature of an already existing Open Bath Furnace process for hot metal production.
Viktor Büttner (HKM)
Accelerating equilibrium calculations for large-scale DRI smelting furnace models – progress with RapidThermo
Johan Zietsman, Thys Nortje, Willem Roos
Ex Mente Technologies, South Africa
The steel industry faces increasing pressure to reduce CO2 emissions and transition away from blast furnaces, while maintaining efficient andprofitable production of high-quality products. To support this transition, comprehensive computational models of new processes are needed. This presentation looks into how thermochemical equilibrium and physical property calculations are combined and accelerated to support largescale computational models of Direct Reduced Iron (DRI) smelting furnaces (DSFs), a key technology for greener steelmaking.
The RapidThermo accelerator concept [1,2] was developed to act as an intermediary between computational models and thermochemical calculators like ChemApp. It stores equilibrium calculation results as geometric objects in an n-dimensional phase diagram. As the phase diagram is populated to cover more composition and temperature ranges, the algorithm interpolates rather than performing more time-consuming direct calculations. This allows large-scale multiphysics models developed with tools like OpenFOAM to benefit from thermochemical calculations to describe high-temperature processes more realistically, without suffering from prohibitive computation times that can run into years or even hundreds of years for large models. Other applications that will benefit from acceleration in the future include dynamic process simulators and advanced process control systems.
In this presentation we share the progress made with RapidThermo implementation since the concept was first published in 2022. The current version provides more acceleration than the original Python implementation, and is now able to provide slag physical properties such as density, electrical conductivity, and viscosity, in addition to equilibrium results that include phase fractions, phase compositions, heat capacity, and enthalpy.
Johan Zietsman (Ex Mente)
Using FactSage for the prediction of powder pack diffusion coatings as protection against attack in high temperature electrolyser environments
Powder pack cementation is a chemical vapour deposition process by which protective elements can be enriched in the surface zone of metallic components. Usually, thermodynamic stable and protective oxide formers, e.g. Al, Cr, Si or Ti, are enriched in the surface zone of an alloy, usually iron- or nickel-based materials, to serve as a donor for the formation of a stable protective oxide scale during service at elevated temperatures. Via the FactSage equilib module the partial pressures of the relevant gaseous species during the powder pack process can be calculated. This allows the prediction of the formed phases on the substrate since the conditions of the process are known, temperature, time and powder mixture composition. The compounds for the powder pack can be chosen according to the results of the preliminary calculations. Post experimental investigations on the metallographic cross sections of the coated specimens reveal the final state of the formed phases (compositions, thicknesses, etc.) and prove whether the predictions by the thermodynamic calculations were correct or whether other reasons, e.g. kinetics, rule the coating formation. Additionally, the FactSage equilib module can be used to predict the stability of the coatings in technical high temperature environments, e.g. of high temperature electrolysers.
Alexander Donchev (DECHEMA)
KilnSimu – Discovering Rotary Kiln Insights
Cassie Früh (GTT-Technologies)
Karri Penttilä (VTT)
Our next-gen process models integrating heat, mass & reaction kinetics
Anna Ravensburg (GTT-Technologies)
End of day
Friday morning (June 6, 9:00-12:00 CEST)
No data? No problem! Tackling missing thermochemical information.
Development of high-Mn steel database
Min-Kyu Paek1 and In-Ho Jung2
1 Institute of Metallurgy, Clausthal University of Technology, Germany
2 Department of Material Science and Engineering, Seoul National University, Korea
Various thermodynamic databases have been developed using the regular solution model to construct phase diagrams. However, the CALPHAD approach without considering strong interactions among the metallic elements and gaseous impurities shows a poor predictability for the practical condition of liquid alloy refining and inclusion evolution in solid steels during casting and heat treatment. Newly developed Twining Induced Plasticity (TWIP) steels contain high-Mn (10-20 mass%) and high-Al (0.5-2 mass%) which are 10-100 times higher concentration compared to the normal Al killed steels. In order to secure both accuracy of liquid solution properties and phase diagrams in this steel grade, thermodynamic evaluation and optimization of all available experimental data on the Fe-Mn-Al-Si core system with impurities such as C, O, N, P and S were performed. The liquid solution properties of the core system and the effect of impurity elements were described by using the Modified Quasichemical Model (MQM). In this model, the strong attraction force was evaluated as the negative Gibbs free energy of the formation of pairs in the pair approximation. The modification of configurational entropy in this model reduces the weight of temperature dependence in the excess Gibbs energy term of liquid solution. It can also affect the stability of all the solid phases to make Gibbs energy balance for liquidus and solidus. This database is stored in the current version of FSStel database in FactSage thermochemistry software. Some examples of the nitride and oxide inclusion formation and phase stability will be presented.
Min-Kyu Paek (TU Clausthal)
CALPHAD modelling of oxide materials for energy conversion and storage
Weiwei Zhang and Ming Chen
Department of Energy Conversion and Storage, Technical University of Denmark
Solid oxide fuel cells (SOFCs) and solid oxide electrolysis cells (SOECs) are promising technologies for efficient energy conversion and storage, utilizing high-temperature electrochemical reactions. Strontium and iron co-doped lanthanum cobaltites (La1-xSrxCo1-yFeyO3-δ, LSCF) show good oxygen ion and electronic conductivity and fast oxygen surface exchange kinetics at temperatures between 600 and 800 °C, and are considered one of the most promising classes of cathode materials for intermediate-temperature solid oxide fuel cells (SOFCs). Despite its technological importance, the phase stability of the LSCF perovskite has not yet been fully mapped out and may be critical for the long-term operation of these materials. For cells with LSCF or LSCF/CGO (CGO: gadolinia-doped ceria) cathodes, partial decomposition of the perovskite phase has been reported as a potential cause of high degradation rates. Additionally, the LSCF perovskite is susceptible to reactions with gas species such as CO2 and water vapor, present in atmospheric air, or species evaporated from stack components (e.g., chromium- or boron-containing gases), which may compromise stability.
In this work, we present a comprehensive thermodynamic database for the multicomponent La-Sr-Co-Fe-O system, established using the CALPHAD (CALculation of PHAse Diagrams) methodology. The modeling integrates experimental data and theoretical calculations to evaluate the phase stability of LSCF as a function of composition, temperature, and oxygen partial pressure. Special attention is given to the influence of Sr and Co content, as well as reduced oxygen partial pressure, on phase decomposition. The database also facilitates the analysis of LSCF reactivity towards gas impurities, particularly under realistic SOFC operating conditions. Our results show that the stability of the LSCF perovskite phase decreases significantly with high Sr or Co content, elevated temperature, or reduced oxygen partial pressure. The insights obtained from the CALPHAD modeling contribute to a better understanding of the stability limits of LSCF and support the optimization of cathode materials for durable and efficient SOFC applications.
Ming Chen (Technical University of Denmark)
EU Database on molten salt reactor fuel system
O. Beneš
European Commission, Joint Research Centre, Karlsruhe, Germany
The Joint Research Centre Molten Salt Database (JRCMSD) for key molten salt reactor fuel and coolant systems has been under development for the past two decades. Initially, efforts were concentrated at the Joint Research Centre in Karlsruhe, focusing on key MSR fuel systems studied globally at that time, including historical MSR concepts. Due to significant data gaps, particularly concerning actinide halides, the database development involved extensive experimental studies to address these gaps. Today, the JRCMSD includes over 120 pseudo-binary systems, encompassing key MSR fuel and coolant systems. It is also being expanded to investigate the effects of corrosion and fission products on fuel properties. Further modelling efforts are being made to couple the selected thermodynamic model for the liquid phase description with other properties such as viscosity and density. The database development is currently a collaborative effort among four organizations, with the JRC leading, and CEA, Orano Group, and TU Delft as partners. It is planned to make the database available to external organizations via the EU Science Hub.
Ondrej Benes (European comission ERC)
From structure to thermodynamic and thermophysical properties of molten salt nuclear fuels: experimental and computational studies at the TU Delft
Anna L. Smitha, Nick ter Veera, Lukasz Ruszczynskia, J.A. Ocadiz-Floresa, John Vlielanda, Sebastian Couweleersa, Aimen Gheribib, Kathy Dardennec, Joerg Rothec, Pier-Lorenzo Solarid, Rudy J. M. Koningsa,e
aDelft University of Technology, Radiation Science and Technology Department, The Netherlands
bConcordia University, Canada
cKARA-INE synchrotron beamline, Karlsruhe Institute of Technology, Germany
dSOLEIL-MARS synchrotron beamline, France
eJoint Research Centre-Karlsruhe, European Commission
Molten salts are receiving increasing attention worldwide as key materials for sustainable and low-carbon energy technologies, including for fission reactors, and in particular for the Molten Salt Reactor (MSR). Because of their appealing thermo-physical properties (e.g. low melting and high boiling points, low vapour pressure, thermal stability, high heat capacity and thermal conductivity etc.), molten salts are considered in MSRs both for the fuel and coolant. Fluoride and chloride salts are to this date the two main candidates, depending on the main objective pursued for the envisaged nuclear reactor, e.g. actinide burner, thorium breeder etc. One main challenge for their future commercialisation is a comprehensive understanding and modelling of the molten salt fuel chemistry, enabling a thorough safety assessment.
Because of the challenges inherent to the work with molten salt materials, which are hygroscopic, highly corrosive at high temperatures, and in the case of nuclear applications radioactive, the available knowledge on the physico-chemical properties is still far from complete. Among these, the local structure properties of the salts at high temperature are particularly relevant, as the formation of short-range order observed in the liquid, has a direct impact on the transport (e.g. viscosity) and excess thermodynamic properties.
In this presentation, I will discuss structural studies of the melt carried out in our research group, that are used as input to develop coupled models of the structural (i.e. chemical speciation) and thermodynamic properties of the molten fuel salt. I will also show examples of our latest efforts to develop models of the density and viscosity of the melt, coupled to the thermodynamic assessments. Developing sound models of the thermochemistry and thermophysical properties of the fuel salt will allow in fine to assess the effect on the fuel properties of e.g. fission and corrosion products accumulation during irradiation in the nuclear reactor.
Anna Smith (TU Delft)
Overview of database development at FZJ
R. Jacob1, M. Ilatovskaia1, V. Lomberg1, A. Morsa1, Z. Su1, J. Qi1, E. Yazhenskikh1, M. Müller1
1 Forschungszentrum Jülich GmbH, Institute of Energy Materials and Devices, Structure and Function of Materials (IMD-1), D-52425, Jülich, Germany
Thermodynamic databases are key to understanding the behaviour of materials in complex systems, in which small changes in conditions can result in large changes of behaviour. This is seen in many applications such as gasification or biomass combustion. Additionally, thermodynamic databases can also be used for complex material design, which may be useful for the prediction of materials which can be used in applications such as thermal storage or electrolysis. Due to the large number of materials, and conditions, experimental-only investigation is unfeasible, meaning accurate and reliable predictions through thermodynamic modelling is required.
In this framework, Forschungszentrum Jülich (FZJ) works on developing thermodynamic databases within several projects such as Verena, Vera, PCM Screening, FesTES, and SaltMe to understand relevant materials and their behaviour. Studied materials include salt, oxide, and metal systems (or combinations thereof) under a range of appropriate conditions.
The presentation is intended to give an overview of the recent work undertaken within these projects, highlighting how the combination of the experimental facilities at FZJ, coupled with our developed thermodynamic databases, are able to give a deeper insight into material behaviour and formation. Some of the highlights include how thermodynamic databases can be used to identify and ‘screen’ phase change materials for use in thermal storage systems which can then be further developed and characterised, how corrosion and sensitivity to air can be overcome in salt-metal material analysis so that a validated phase diagram can be established, and how developing phase diagrams for salt-oxide systems can be used to improve gasifier performance to avoid unwanted products during operation.
Rhys Jacob (Forschungszentrum Jülich)
Calphad Optimizer
Bruno Reis (GTT-Technologies)
Florian Tang (GTT-Technologies)
Farewell
Stephan Petersen (GTT-Technologies)
Moritz to Baben (GTT-Technologies)
End of day
This schedule is almost final, but last-minute adjustments may occur due to speaker availability or organizational needs. We appreciate your understanding!
WHAT TO EXPECT AT THE 2025 USERS’ MEETING
New venue: Forum M, Aachen
The 2025 meeting will take place at Forum M in the heart of Aachen. The venue is centrally located yet idyllically situated above the historic rooftops. It lies between the Elisenbrunnen, the cathedral and the town hall, with a beautiful view of the old town from the roof terrace and a unique networking atmosphere. The central location offers many hotels and accommodations within walking distance and excellent public transportation connections.
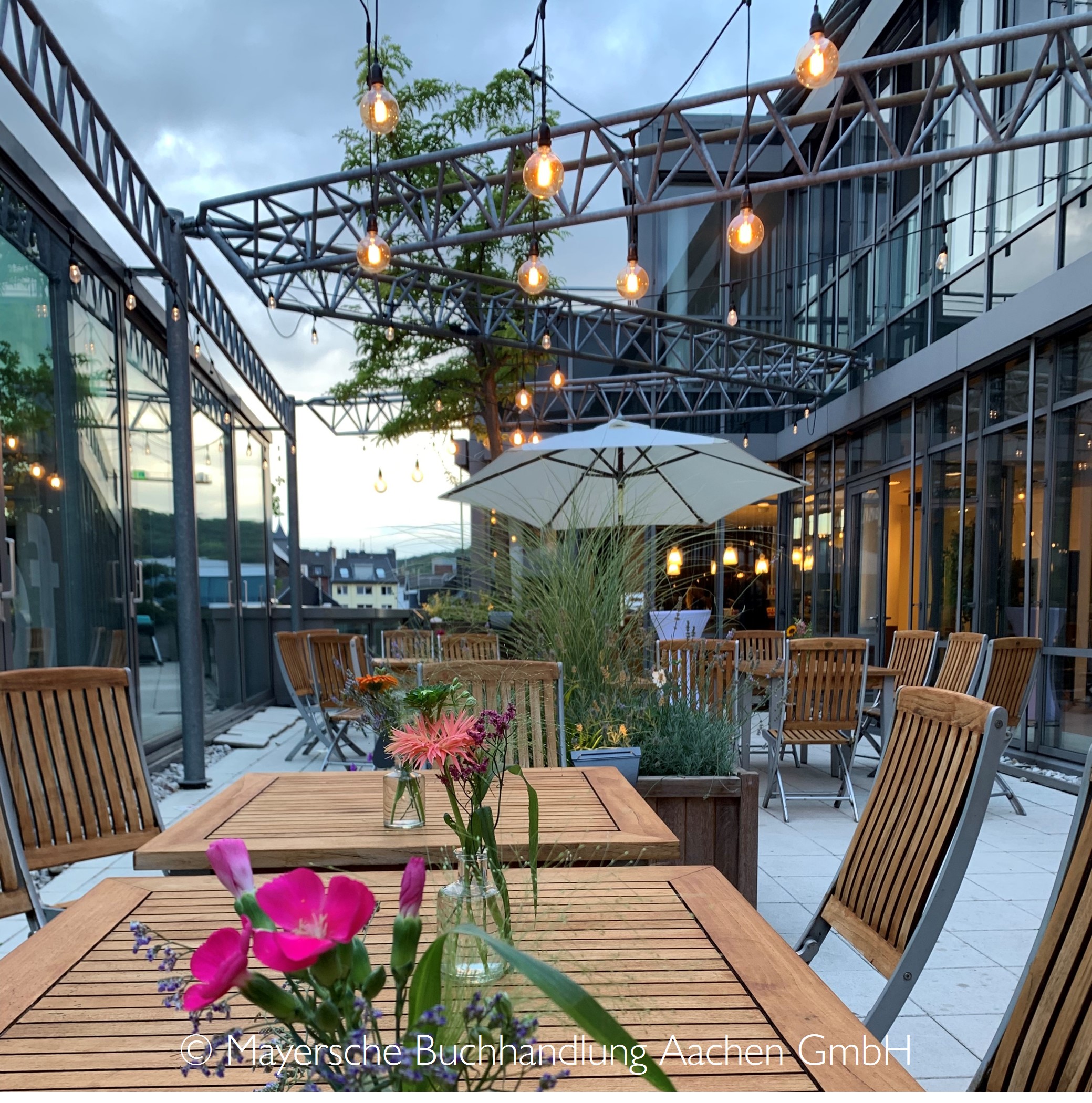
Hybrid experience: Join in-person or online!
We will be streaming the presentations from all sessions for online attendees. Building on the experience from our hybrid Users’ meeting last year, we are working to make this experience as smooth as possible.
As a result, online attendees can expect live-streamed talks and discussions as well as access to selected materials after the event.
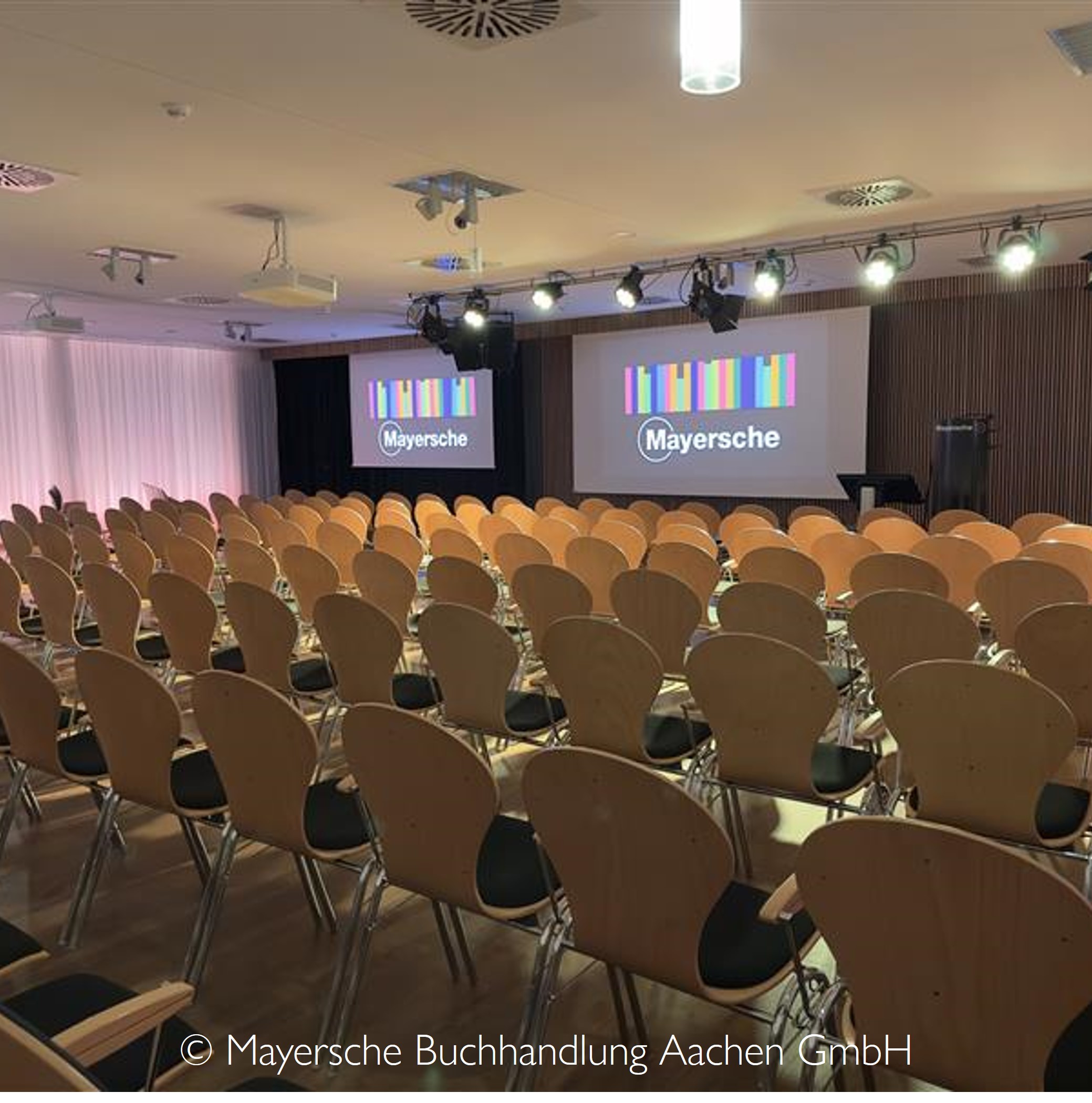
Social program
In addition to the technical sessions, the Users’ Meeting will offer plenty of opportunities for informal exchange and networking. Throughout the event, you’ll be able to meet other users and the GTT-Technologies team in person, during sessions, breaks, and casual moments. One of the highlights: relaxed conversations on the rooftop terrace with its unique view over Aachen’s old town.
A group dinner is planned for Thursday evening (June 5) to continue both technical discussions and informal exchange in a friendly atmosphere. The dinner will take place at 19:30 at Living im Magellan, a restaurant located in the center of Aachen and just a short walk from the venue.
Please note: Participation is optional and at your own expense.
If you would like to join us for dinner at the last minute, please speak to us during the Users’ Meeting. We will do our best to make it possible.
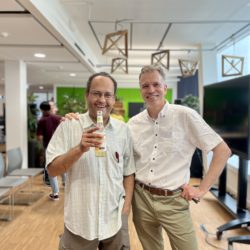
REGISTRATION
Registration is now closed.
For any last-minute attendance, whether in-person or online, please send us an email. We will do our best to respond quickly and send you the Zoom links in time.
If you’re nearby and know us personally, feel free to reach out or stop by; we’re confident we’ll find a seat for you.
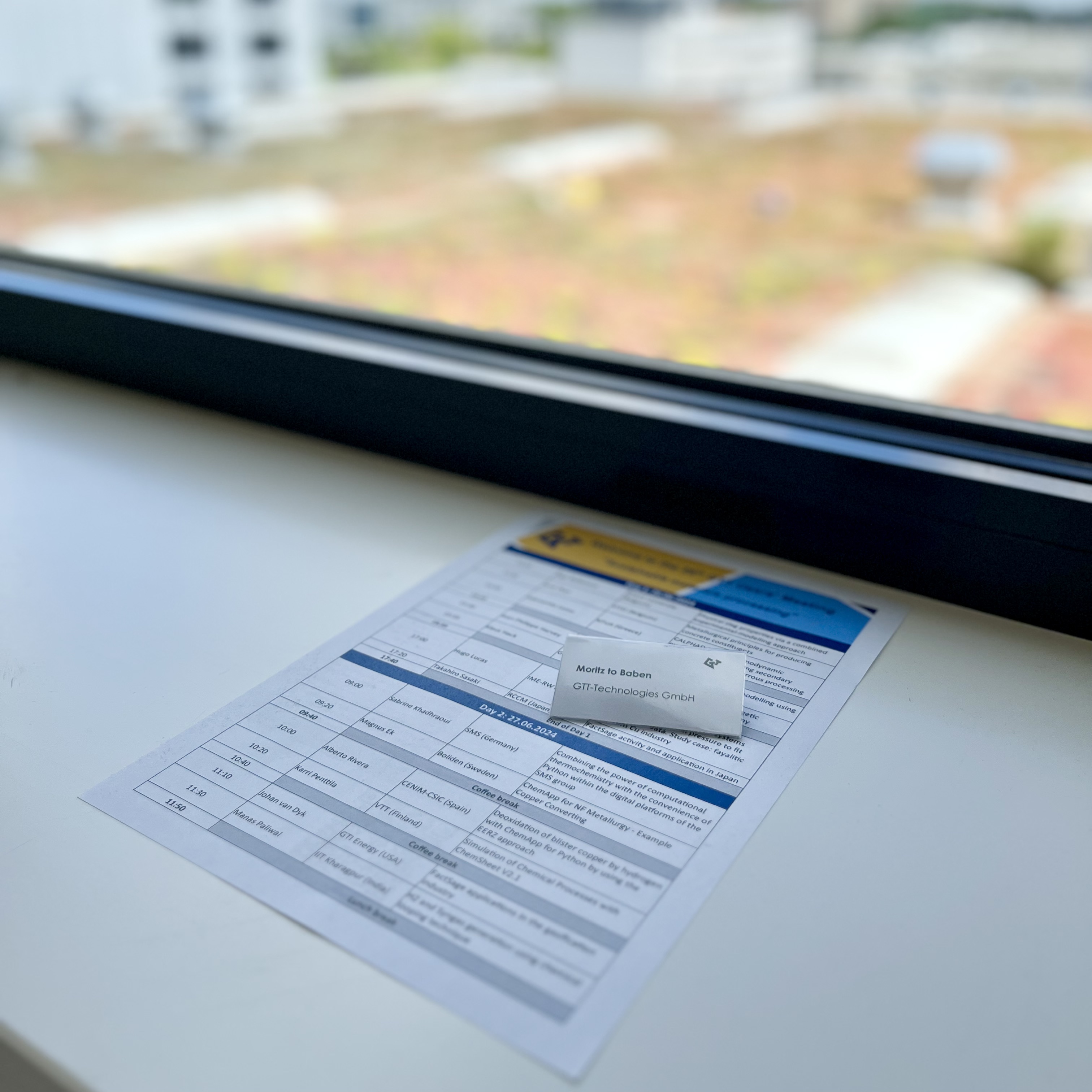