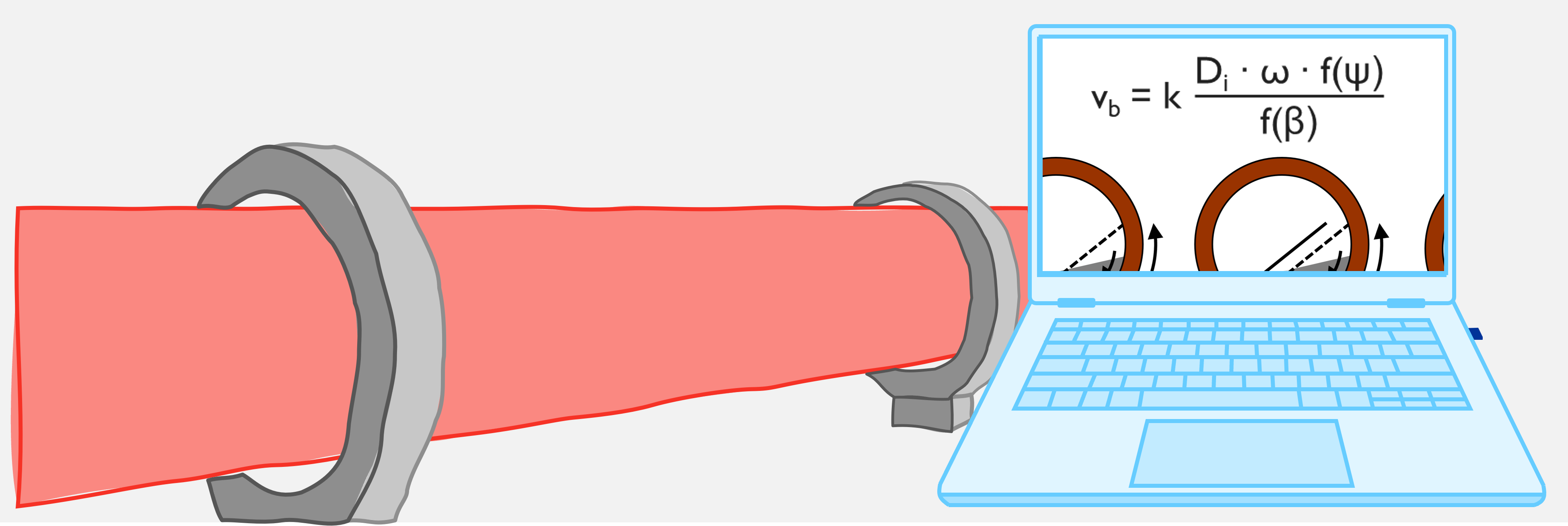
Documentation & scientific background to support your advanced kiln simulations.
This section provides detailed resources to help users better understand KilnSimu, its features, and underlying principles. This page includes access to the official documentation (coming soon), research papers, and key background information that explain the core functionalities and technical aspects of the software.
1. DOWNLOAD AREA
1.1 KilnSimu Documentation
This section will be available soon. Please check back later for the official KilnSimu documentation.
1.2 System requirements
Detailed system requirements for running KilnSimu will be added here. In the meantime, you can review the specifications for the optional ExtendSim interface via the following link: ExtendSim system requirements.
1.3 References & Papers
Rotary kilns are crucial in many industries such as cement and pigment manufacturing, as well as in chemical recovery processes like lime recycling in Kraft pulping. KilnSimu is a versatile simulation software designed to model rotary kiln applications, including slurry processing and other condensed mixtures. In one study, the software was used to simulate a lime kiln powered by either natural gas or gas from bark gasification. KilnSimu models complex chemical systems, incorporating thermodynamic equilibrium and reaction kinetics. It helps optimize process parameters like fuel consumption and production capacity, contributing to more efficient operations across various industries. The software’s ability to handle multi-phase chemical systems makes it valuable for process analysis and optimization.
Keywords: KilnSimu, Lime kiln, Thermodynamic equilibrium, Reaction kinetics, Process simulation
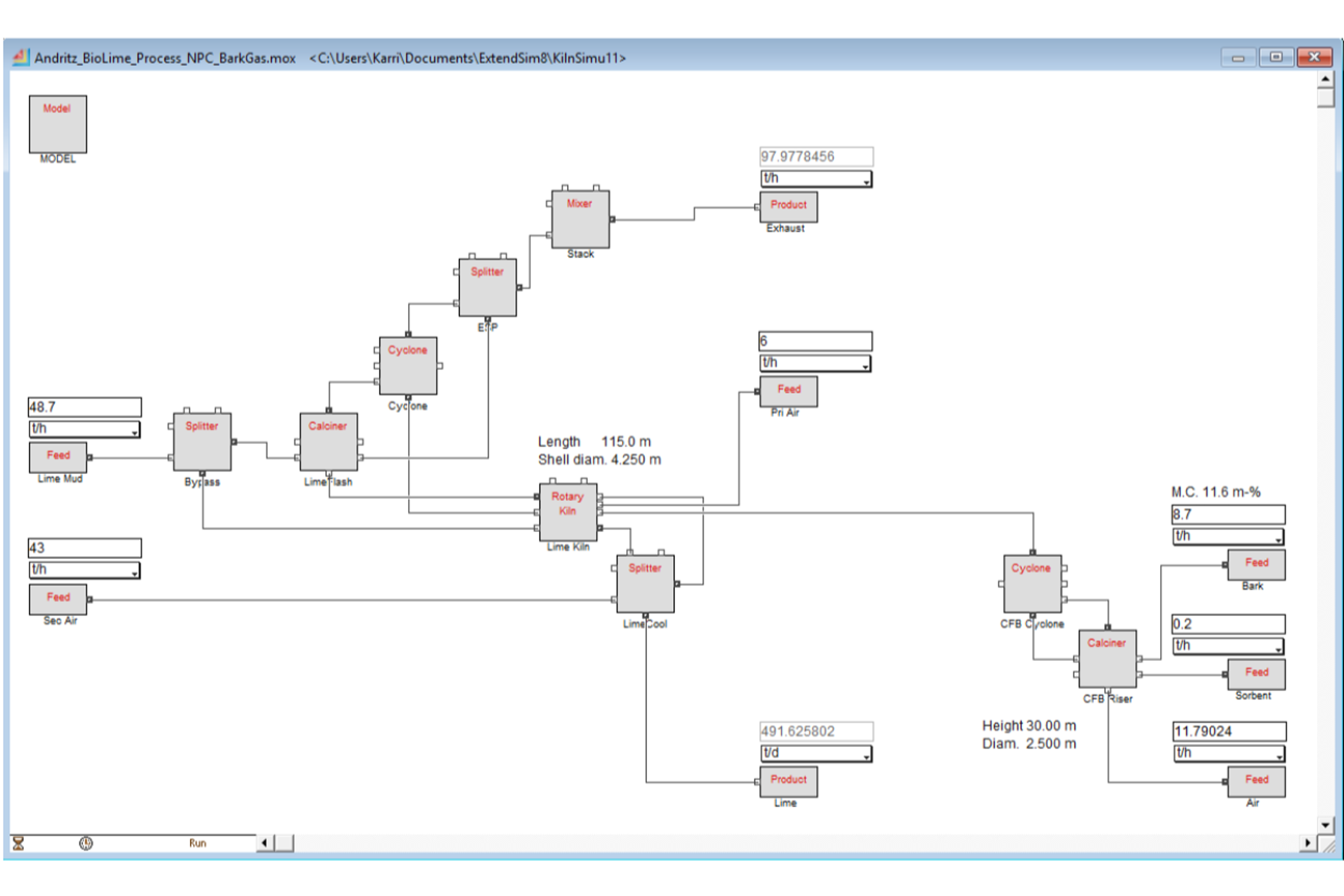
Rotary kilns continue to be integral in industries like cement manufacturing, where they facilitate processes such as clinker formation and the thermal treatment of various raw materials. The simulation tool KilnSimu has been applied to predict key aspects of kiln performance, including the formation of cement clinker crystals and the circulation of sulfate and chloride species. The software calculates axial temperature profiles and phase compositions within the kiln bed and gas flows. By optimizing fuel consumption and examining the effects of different fuels, KilnSimu supports improved operational efficiency. The model also aids in refining the kiln’s gas circulation and geometry, ultimately contributing to more energy-efficient cement production.
Keywords: KilnSimu, Cement kiln, Gibbs energy minimization, Sulfate circulation, Fuel optimization
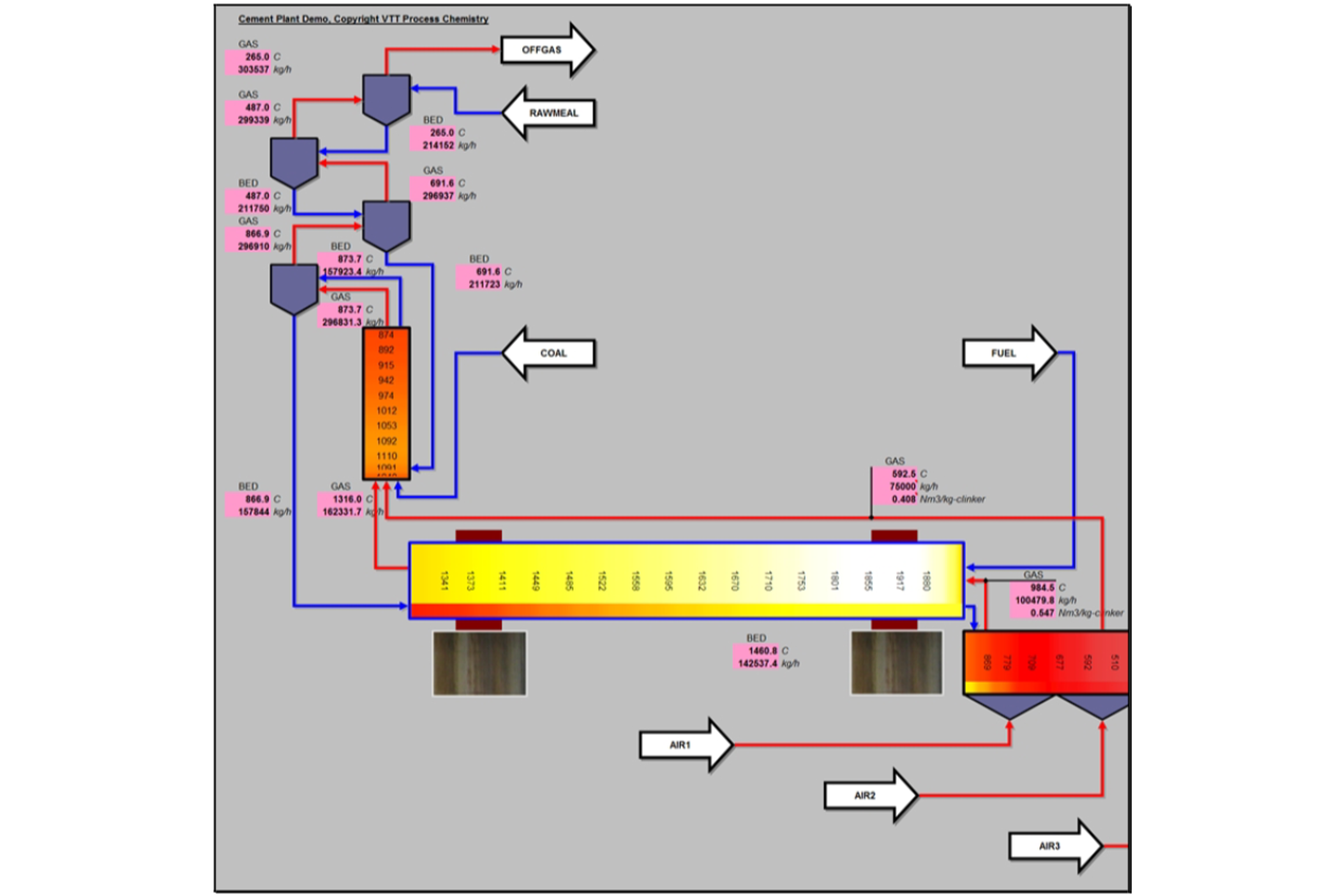
This paper investigates the distribution and accumulation of non-process elements (NPEs) in a lime kiln fired with renewable product gas, using KilnSimu for thermodynamic modeling. The study aimed to predict the effects of NPEs from the bark product gas on the lime kiln and its impact on lime quality. The modeling showed that for easily volatilized components like alkali chlorides, optimizing reaction rate parameters is essential. Based on the model and measurement results, the enrichment of NPEs in lime was not a significant issue in the studied case. However, the actual enrichment factors depend on factors such as lime mud composition, make-up lime, and the product gas involved. This work contributes to process optimization and environmental management in lime production.
Keywords: Lime kiln, NPEs, Renewable gas, Alkali chlorides, Process modeling
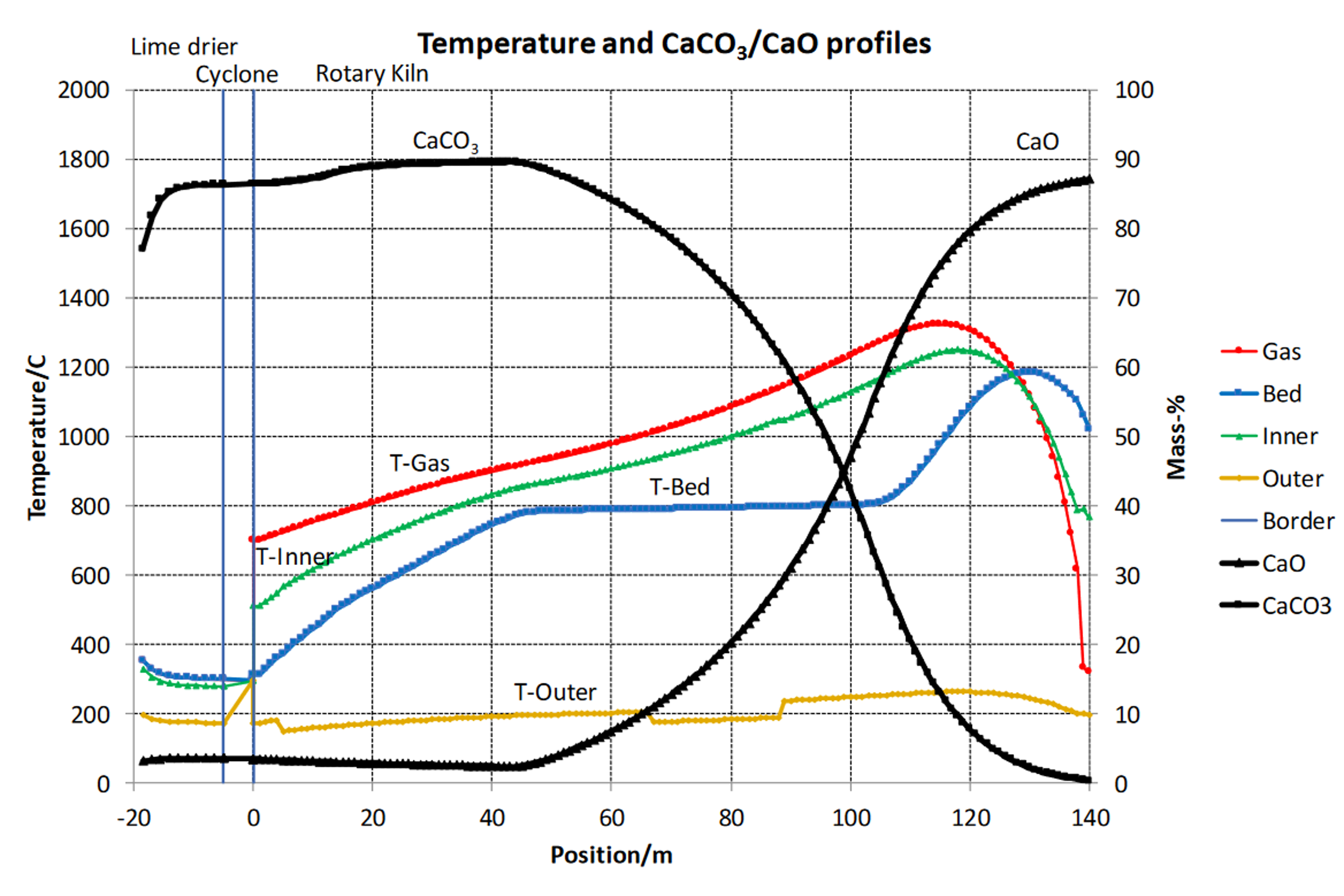
cyclone and lime kiln.
As industrial automation increases, simulation studies become critical for process optimization. This paper evaluates simulation methods for a calcination kiln process, presenting both a static first-principles model and a dynamic “black-box” model. These simulations provide valuable insights into the process phenomena that influence kiln operations. The study discusses the economic motivations for using simulations to improve plant operations and bring processes closer to optimal performance. By applying these models, it is possible to enhance the understanding of key factors affecting calcination and develop more effective control algorithms. This approach is valuable for improving both operational efficiency and economic outcomes in industrial calcination processes.
Keywords: Simulation, Calcination kiln, Process modeling, Control algorithms, Economic evaluation
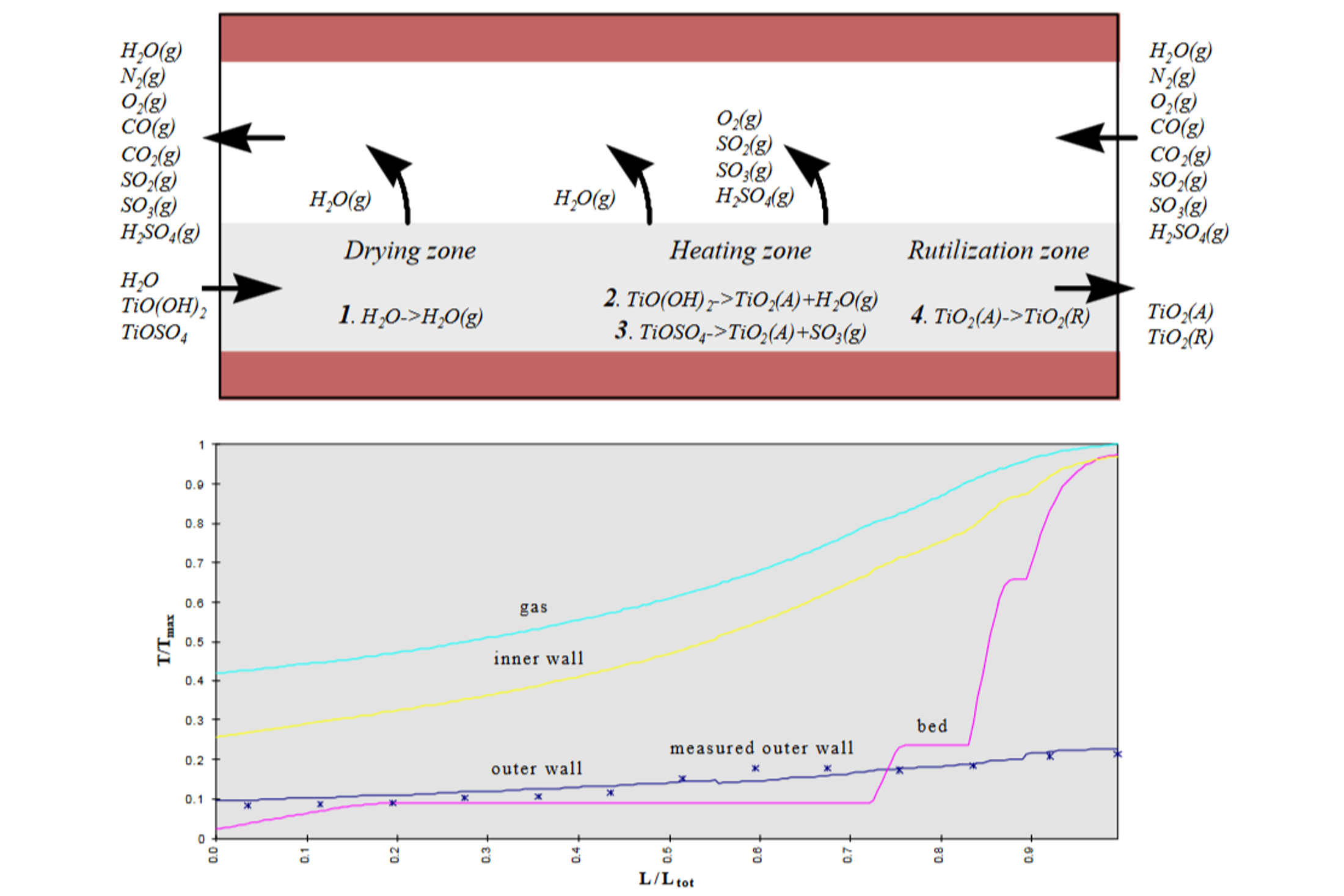
The application of Gibbs free energy minimization for modeling thermochemical processes in rotary kilns is a sophisticated method used to analyze chemical reactions and phase changes in various industrial settings. KilnSimu utilizes this method to simulate the thermal and chemical processes in cement clinker manufacturing. The program integrates the iterative solution of balance equations with Gibbs energy calculations, providing a detailed analysis of mass and heat flows within the kiln. By incorporating reaction rate constraints, the model captures the necessary kinetics. In a case study, the impact of pure oxygen addition on the specific heat consumption during cement clinker production was assessed, demonstrating the potential for process optimization.
Keywords: KilnSimu, Gibbs energy, Rotary kiln, Cement clinker, Oxygen injection

The cement manufacturing process is vital globally, and optimizing it is key to reducing energy consumption. This study, supported by the Japanese Ministry of Economy, Trade, and Industry, developed simulation technologies to evaluate energy use in cement production. The project utilized tools like KilnSimu and Fluent to model the chemical reactions and temperature profiles within rotary kilns. The simulations examined factors such as leakage air, fuel-to-air ratio, clinker cooler efficiency, and kiln dimensions. Among these, improving clinker cooler efficiency proved to be the most effective strategy for energy reduction. This study provides insights into energy-efficient practices for cement manufacturing.
Keywords: Cement process, Simulation, KilnSimu, Energy efficiency, Clinker cooler
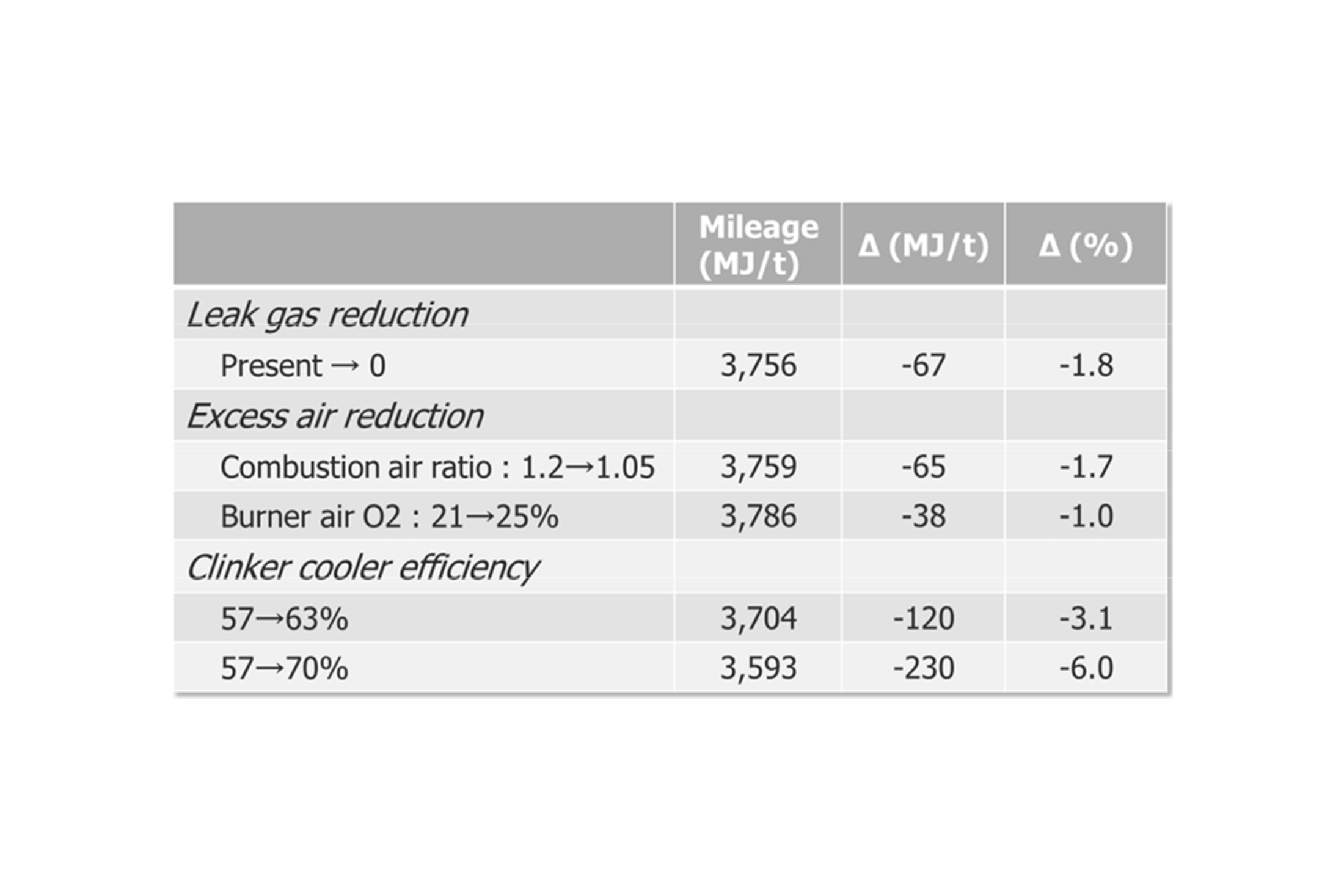
2. BACKGROUND INFORMATION
KilnSimu offers detailed simulations of rotary kilns by considering multiple aspects of kiln behavior and thermal dynamics. This section provides background on key operating modes, axial calculation zones, bed movement types, and heat transfer mechanisms, all of which are essential for understanding the functioning and simulation of rotary kilns.
2.1 Operating modes
Counter-current mode
In the counter-current mode, material is introduced at the cold “feed end” of the kiln, where it is gradually heated by hot gases flowing in the opposite direction from the “burner end”. This heat transfer causes the desired chemical reactions, and the final product is removed from the hot end. KilnSimu allows for flexible modeling of feed and gas flows, where there can be multiple feed positions along the kiln, with at least one bed feed at the feed end and one gas feed at the burner end. This mode is commonly used in most industrial kilns.
Co-current mode
In co-current mode, both the feed material and the hot gas enter the kiln from the same end and move in the same direction. The material is heated by the gases as they flow together towards the exit, and the final product is removed at the hot end. KilnSimu supports co-current flow setups, where the gas flow direction is reversed compared to counter-current mode, and the burner end and feed end coincide. This mode is less common but can be beneficial in certain processes requiring specific heat transfer dynamics.
2.2 Axial calculation zones
KilnSimu divides the rotary kiln into axial calculation zones. Within each zone, temperatures and phase compositions of the material bed and gas are assumed to be constant. The volume elements within these zones are treated as open thermodynamic systems, exchanging mass and heat. The system achieves equilibrium by minimizing Gibbs energy, considering both mass and heat transfers between elements and their surroundings. The material bed is divided into reactive and inert subsystems, with reaction rates calculated based on Arrhenius equations. Energy and mass balances converge to provide a steady-state solution, with the radial movement of the bed dependent on the kiln’s properties and angular velocity.
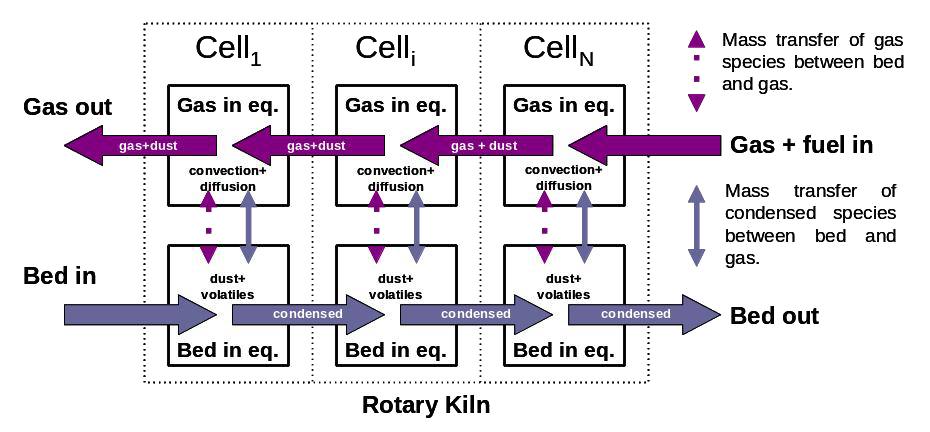
Axial temperature profiles
Simulations provide detailed axial temperature profiles for the bed, gas, and inner and outer kiln walls. Phase compositions are also calculated along the kiln’s length. These profiles help optimize fuel consumption, adjust material feed rates, study the effects of different fuels, and explore factors like gas circulation and kiln geometry. KilnSimu is especially useful for scaling up kiln operations.
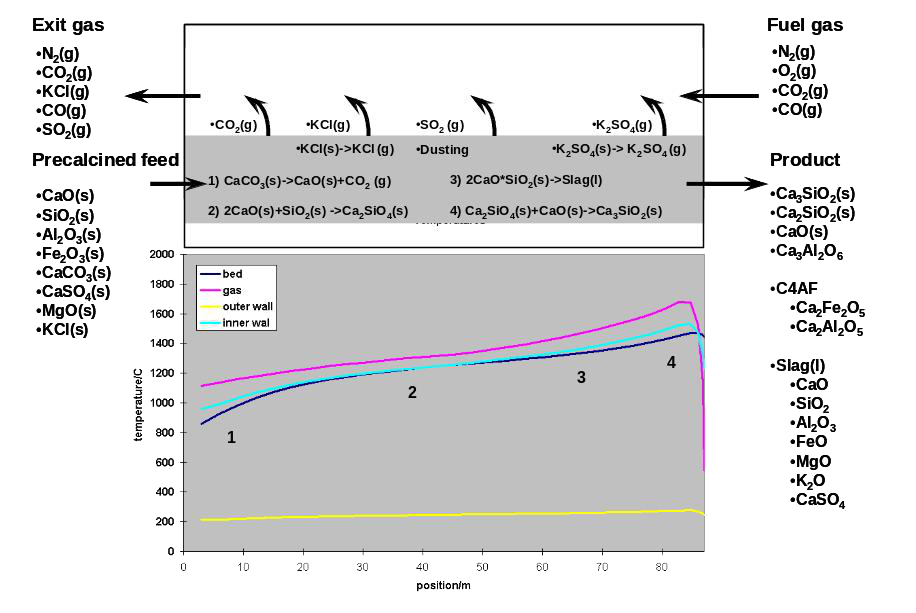
(from: Simulation studies of a calcination kiln process, Ketonen et al.)
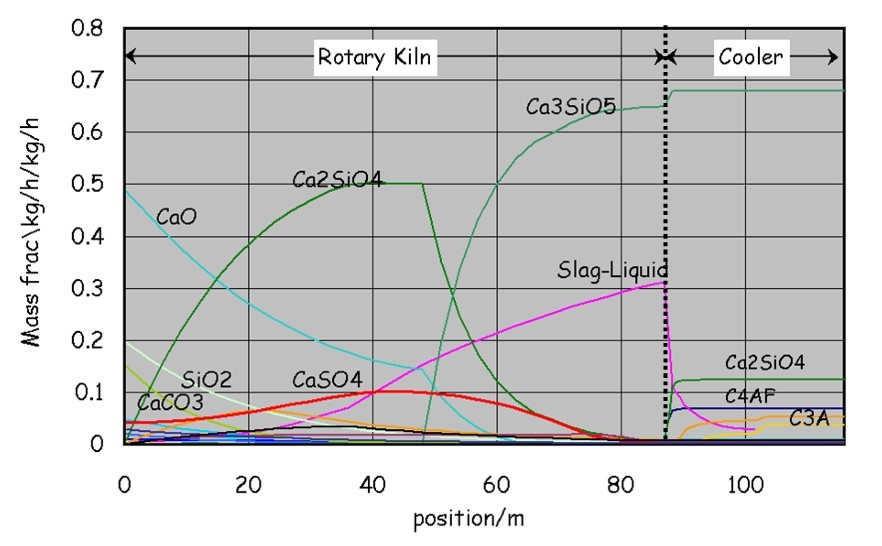
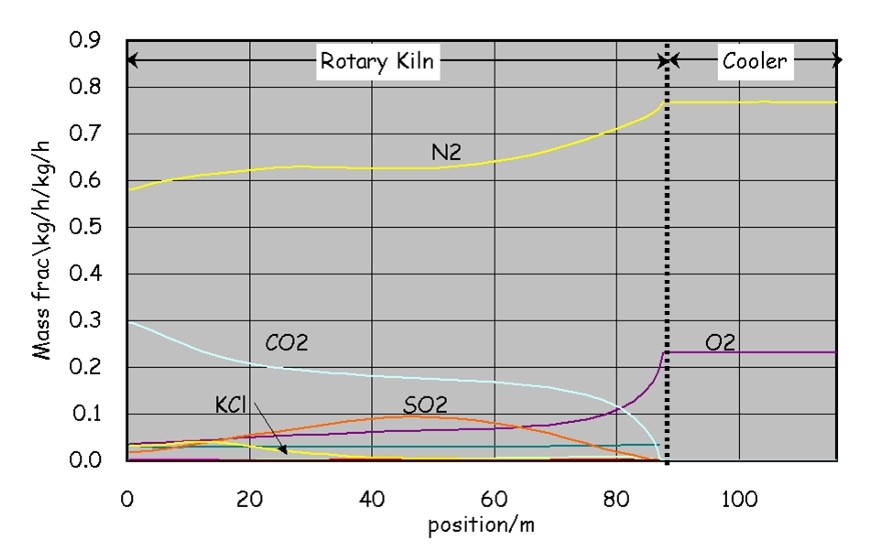
Typical results for a pre-calcined cement kiln (from: KilnSimu and Cement Applications, Pentillä K.)
2.3 Bed movement types
KilnSimu allows for three types of bed movement, depending on the bed properties and kiln rotation speed:
Sliding
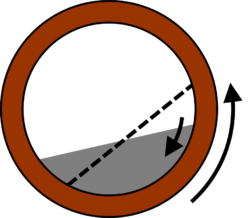
The bed slides along the kiln surface at lower rotational speeds.
Slumping
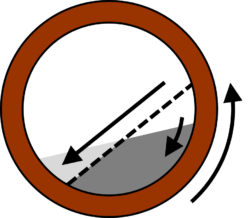
Intermediate movement where the bed partially shifts.
Rolling
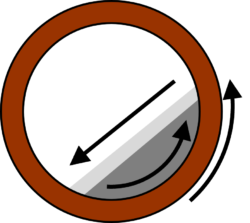
The bed rolls continuously at higher rotational speeds.
The bed velocity (vb) in the kiln is a function of:
- Inner diameter (Di)
- Rotational speed (ω)
- Inclination angle (ψ)
- Dynamic angle of repose (β)
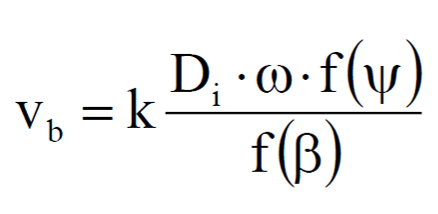
In addition, the bed velocity is inversely proportional to the height of the bed or the hold up of the kiln.
2.4 Heat transfer mechanisms
KilnSimu models several direct as well as indirect heating mechanisms. These heat transfer mechanisms are crucial for accurate thermal modeling within KilnSimu, enabling efficient simulation of the kiln’s heating process.
Convection
Heat transfer from gas to a surface (kiln wall or the surface of the bed).
Conduction
Heat transfer from wall to bed surface that is in contact for certain time with the wall.
Radiation
Heat transfer between surfaces (e.g., bed and inner wall), modeled as radial radiation. Radiation depends on view factor between them, which is a function of the geometry and emissivity of the surfaces.
The emissivity of the gas is calculated from combustion products such as CO, CO2, H2O and for other polyatomic molecules such as SO2. Small particles like soot and ash also contribute to heat emission.
KilnSimu considers only radial radiation.