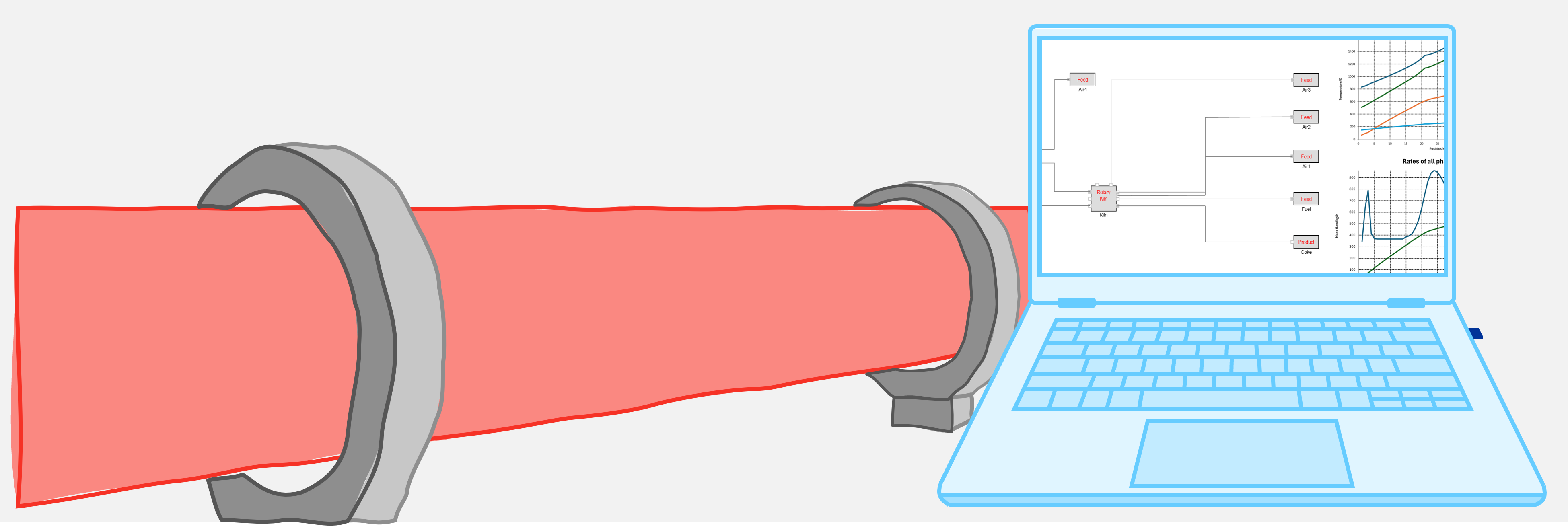
Industrial solutions: From simulation to actionable results.
KilnSimu empowers users across industries to simulate and optimize rotary kiln processes, addressing diverse applications in production, calcination, reduction, and recycling. By accurately modeling temperature profiles, phase transformations, and material flows, KilnSimu provides actionable insights into rotary kiln operations. This enables the anticipation and resolution of potential challenges early in the design phase, facilitating faster project execution with reliable, data-supported decisions.
Whether simulating a cement kiln or optimizing processes like the calcination of coke, KilnSimu delivers tailored insights for each unique application. The software visualizes critical parameters such as gas, bed, and wall temperatures, phase conversion rates, and the behavior of specific components across the kiln.
KilnSimu’s wide range of industrial applications:
Production of activated carbon
Production of alumina
Production of cement
Calcination of clay
Calcination of coke
Calcination of limestone
Calcination of TiO2
Production of lithium carbonate from spodumene
Metal recycling
Reduction of ilmenite
Reduction of zinc dust
Reduction of laterite ore
Waste incineration
Waste & Wood pyrolysis
To illustrate its broad applicability, this section outlines key use cases across various industries. Selected highlight publications further demonstrate the impact of KilnSimu in practice, showcasing its role in solving complex challenges in rotary kiln processes.
PRODUCTION
Tailored simulations for efficient manufacturing
KilnSimu’s simulation capabilities extend to a wide range of production processes, from carbon activation to cement clinker manufacturing. By providing insights into chemical reactions, energy use, and phase transformations, the software enables users to refine operational efficiency, reduce costs, and achieve sustainable production goals. It allows for rapid testing of alternative materials, fuels, or configurations, supporting innovation and enabling quick prototyping to explore new design possibilities.
Activated carbon
Simulation of carbonization and activation steps for industrial production.
Alumina
Optimization of calcination and sintering processes for aluminum production.
Cement
Comprehensive modeling of clinker production, including temperature profiling and gas composition analysis.
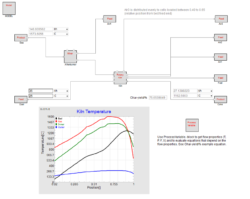
Application example: Cement kiln workflow
A detailed example of a cement kiln application is used to demonstrate the capabilities of KilnSimu. The workflow is illustrated step by step with extensive screenshots showing how the software models and analyzes critical aspects of rotary kiln processes.
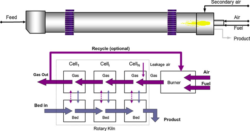
Computation of steady state thermochemistry in rotary kilns: Application to the cement clinker manufacturing process
Meyer et al. apply advanced Gibbs energy minimization methods to model cement clinker manufacturing processes. The study evaluates the effects of oxygen addition at the main burner on heat consumption, providing insights into optimizing energy usage and chemical reactions during clinker production.
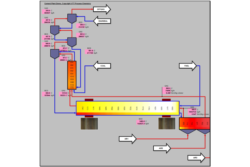
Kilnsimu and Cement Application. Advanced Gibbs Energy Methods for Functional Materials and Processes
Penttilä et al. showcase how KilnSimu was successfully used for modeling clinker production processes, including the prediction of cement clinker formation, sulfate and chlorine behavior, and energy optimization through various fuels.
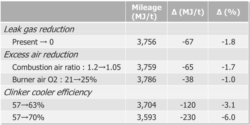
Development of Simulation Technology for Cement Manufacturing Process
Yokota et al. focuses on using KilnSimu and additional simulation tools like FactSage to analyze chemical reactions and heat balances in cement manufacturing.
Lithium carbonate
Thermal processing of spodumene ore for lithium-ion battery production.
CALCINATION
Refining calcination processes for improved efficiency
Calcination is a critical step in many industries, requiring precise control of temperature gradients and material behavior. KilnSimu delivers advanced modeling tools to optimize these processes, offering insights into phase transformations, energy consumption, and the impact of different fuels. By detecting and resolving inefficiencies and bottlenecks in operations, KilnSimu optimizes energy use, significantly lowering operational costs and improving resource management by fine-tuning material inputs and process settings. From ceramics to white pigments, KilnSimu supports sustainable and efficient calcination operations.
Clay
Simulation of clay calcination processes for ceramics and aluminum production.
Coke
Modeling the thermal decomposition and transformation of coke for industrial use. Analyze temperature gradients, phase transformations, and component behavior.
Limestone
Detailed simulations of lime kilns for steelmaking and pulp and paper industries.
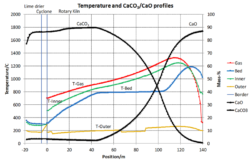
Modelling of non-process elements in a lime kiln burning renewable product gas
Penttilä et al. investigate the distribution and accumulation of non-process elements (NPEs) in a lime kiln fired with renewable product gas, using KilnSimu for thermodynamic modeling.
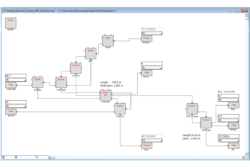
Advanced Thermochemical Process Model of Rotary Kilns: Kilnsimu
Penttilä et al. investigate lime kiln processes using KilnSimu, comparing natural gas and renewable product gas as fuels. The results demonstrate the software’s capability to optimize lime production.
TiO2
Simulation of calcination processes for producing white pigments.
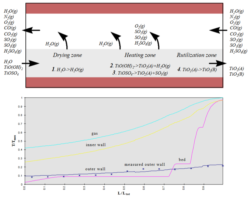
Simulation Studies of a Calcination Kiln Process
Ketonen et al. evaluate the economic and process optimization benefits of using simulation in calcination processes, including temperature gradient analysis and phase transformations.
REDUCTION
Optimizing energy-intensive reduction applications
Reduction processes in rotary kilns are crucial for extracting and refining valuable metals. KilnSimu offers detailed simulations to optimize these energy-intensive operations, enabling precise control of material transformations and energy use. Whether producing ferronickel, titanium slag, or recovering zinc, the software helps industries achieve sustainable and cost-effective results.
Ilmenite
Modeling the reduction of ilmenite to produce titanium slag or synthetic rutile.
Laterite ore
Ferronickel production through the reduction of laterite ore.
Zinc dust
Simulation of Waelz kiln operations for zinc recovery.
RECYCLING & WASTE
Sustainable solutions for circular economy processes
Efficient recycling and waste management are critical for sustainable industrial practices. KilnSimu provides precise simulations of rotary kiln processes, helping industries recover valuable metals, convert waste into energy, and produce biochar through pyrolysis. By modeling hazardous scenarios to assess and mitigate risks before implementation, KilnSimu facilitates adherence to environmental standards by optimizing emissions control and enhances workplace safety by anticipating and addressing potential vulnerabilities. These tools enable cost savings, reduced emissions, and optimized resource utilization.
Metal recycling
Optimization of kiln-based processes for recovering valuable metals.
Waste incineration
Modeling combustion and gasification for efficient waste-to-energy processes.
Waste & wood pyrolysis
Simulation of pyrolysis processes for biochar production and waste management.