Explore advanced kiln simulation: Core features, process units, and more.
KilnSimu offers advanced kiln simulation features, making it a powerful tool specifically designed for rotary kiln modeling incindustries such as cement, lime, and metallurgy. It allows users to analyze and optimize process parameters to improve efficiency, product quality, and energy consumption.
Applications range from improving cement clinker production to refining calcination processes, improving ore reduction methods, and optimizing recycling and waste-to-energy operations.
Advanced kiln simulation for critical insight and comprehensive results.
Unlike traditional CFD models that focus on three-dimensional flow dynamics, KilnSimu uses advanced kiln simulation features to provide insight into the chemical composition and phase transformations occurring along the kiln. By combining advanced thermodynamic equilibrium calculations with kinetics, KilnSimu bridges the gap between theoretical modeling and practical industrial applications. This approach empowers users to make data-driven adjustments, test alternative fuels or feedstocks, and ultimately achieve better operational outcomes in a range of industrial scenarios.
This overview highlights:
CORE FEATURES
Our thermodynamic expertise tailored to industrial kiln applications
KilnSimu’s advanced features enable users to understand, predict, and control kiln operations. By integrating state-of-the-art equilibrium calculations with kinetic modeling, the software provides insight into the complex processes occurring inside rotary kilns. With its advanced kiln simulation features, KilnSimu helps users optimize production efficiency, reduce emissions, or improve product quality, enabling informed decision-making based on scientifically validated results.
Additionally, KilnSimu serves as an effective training aid for new personnel, offering a hands-on learning platform to simulate real-world scenarios, thereby enhancing technical onboarding and bridging knowledge gaps efficiently.
Equilibrium calculations
ChemApp‘s robust equilibrium solver accurately calculates chemical equilibria along the kiln path.
Kinetic modeling
Integrates equilibrium calculations with kinetic models, supported by a tailored database for kiln processes.
Composition & structure
Provides composition and crystal structure changes in the kiln for invaluable process insight.
Simulate entire plant setups with multiple configurable process units.
Fine-tune input parameters
Adjust key input parameters at each kiln step for greater control, allowing for rapid assessment of new materials, fuels, or process configurations.
Povides detailed results, including gas and solid compositions, at each stage in the kiln.
Full process support
Supports counter-current and co-current operation modes, all bed movement types, and comprehensive heat transfer mechanisms, including convection, conduction, and radiation.
Interactive Training Aid
Acts as a training tool by allowing personnel to simulate kiln operations in a virtual environment, accelerating onboarding and skill acquisition without disrupting production workflows.
Benefit from expert guidance provided by our team with extensive experience in industrial kiln processes.
PROCESS UNITS
From preheater to cooler: model your entire process
KilnSimu supports a wide range of process units. Together, they allow comprehensive simulation of a complete kiln system. The software is equipped to model key components such as preheaters, calciners, kilns, and coolers. This versatility allows users to simulate complex setups and gain valuable insight into the interaction of different system parts, ensuring a holistic approach to process optimization.
Rotary kiln
Simulates the rotary kiln process for accurate material and heat flow dynamics.
Clinker Cooler
Models a grate clinker cooler for effective heat recovery and clinker cooling.
Calciner
Represents a precalciner duct or pipe for the CaCO3↔CaO+CO2(g) reaction.
Cyclone
Separates particles from the gas flow to ensure accurate phase distribution.
Fluidized Bed
Allows a solid granular material to behave like a fluid by passing a fluid upward through at controlled velocity.
Mixer
Combines multiple flows with an energy balance for consistent process integration.
Splitter
Splits one or more flows into two flows while maintaining energy balance and process accuracy.
Tearing
Initializes intermediate flows and helps to achieve convergence.
Feed
Defines and initializes the input feed flow to the system.
Prod
Represents the final product flow for downstream analysis.
MODEL INPUTS & OUTPUTS
Capture every detail: inputs for precision modeling & detailed outputs for process optimization
KilnSimu requires a number of input parameters to accurately simulate rotary kiln behavior. These inputs include feed compositions, thermodynamic data, process conditions, and operational parameters. The outputs provide insights that enable targeted optimization of your process.
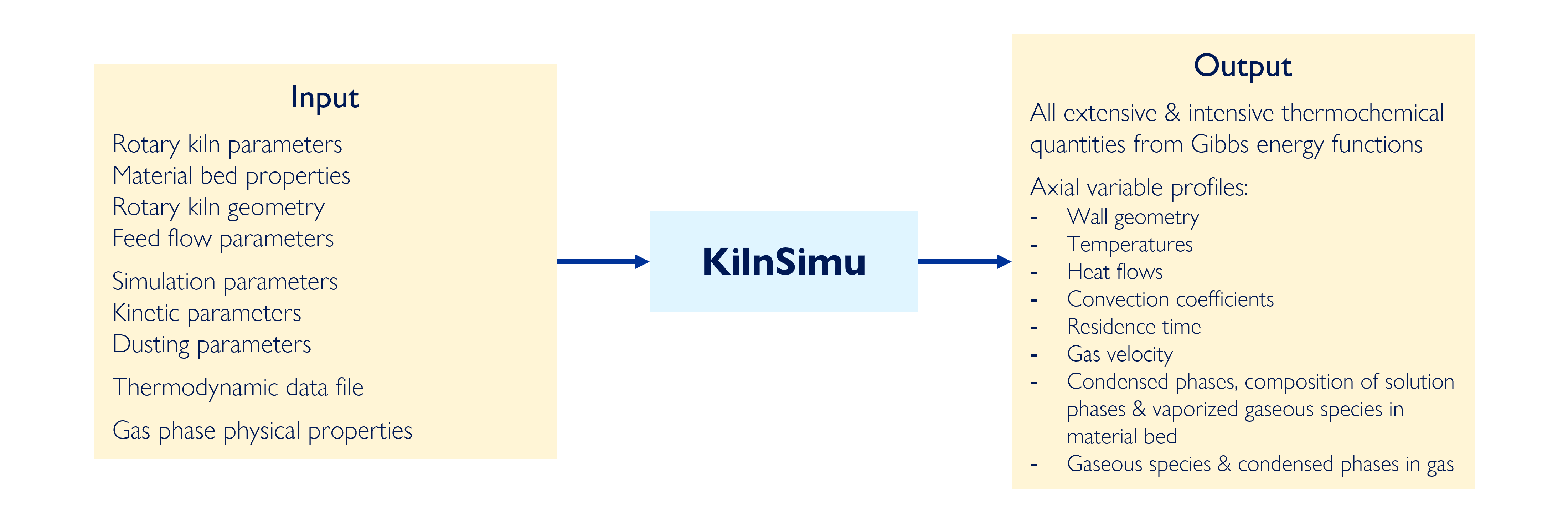
Input parameters
Setting up a simulation in KilnSimu involves defining a variety of parameters that capture the unique characteristics of each process. User input includes feed material properties, flow rates, fuel type, and kiln geometry. This detailed customization ensures that the software accurately represents real-world conditions, enabling accurate predictions and effective decision-making for process improvements.
To set up a KilnSimu simulation, various parameters and properties must be defined:
Rotary kiln parameters
- Rotational speed
- Inclination
Material bed properties
- Static and dynamic angle of repose
- Density
- Emissivity
- Conductivity
Feed flow parameters
- Temperature
- Pressure
- Amounts of one or more feed species
Rotary kiln geometry
Geometry data may contain one or more wall sections and each section contains:
- Length
- Outer wall diameter
- Steel layer and one or more refractory layers
of given thickness and conductivity
Simulation parameters
- Number of iterations
- Convergence criterion
Kinetic parameters
Reaction rate coefficients for each phase in material bed and gas:
- Frequency factor
- Activation energy
- Kinetic model
Dusting parameters
- Dusting coefficient for each phase
ChemSage format data-file
Containing the definitions and thermodynamic properties of system phases and phase constituents
Gas phase physical properties
- Conductivity parameters
- Viscosity parameters
Output parameters
KilnSimu generates a comprehensive set of outputs that provide valuable data to support process analysis and optimization. Thermodynamic quantities such as temperature, pressure, and heat flow are provided alongside axial profiles that detail the progression of variables throughout the kiln. This level of detail allows users to fine-tune their operations and address specific challenges with data-driven solutions.
The thermodynamic model provides a large amount of numerical data to the user. In principle, from the Gibbs energy functions, all extensive and intensive (locally measurable) thermochemical quantities can be calculated.
The axial variable profiles, for which Excel plots are generated, include:
Wall geometry
Temperatures
Heat flows
Convection coefficients
Residence time
Gas velocity
Condensed phases
in material bed
Solution phase compositions
in material bed
Vaporized gaseous species
in material bed
Gaseous species in gas
Condensed phases in gas
OPERATING MODES
Flexible approaches: adaption to your operating needs
The software supports multiple operating scenarios, making it suitable for a wide range of industrial applications. Whether simulating continuous or batch operations, KilnSimu’s advanced kiln simulation features adapt to the requirements of your process. Its flexibility ensures that it can accurately replicate different production strategies, supporting both standard and highly specialized workflows.
Counter-current mode
In the counter-current mode, material is introduced at the cold “feed end” of the kiln, where it is gradually heated by hot gases flowing in the opposite direction from the “burner end”. This heat transfer causes the desired chemical reactions, and the final product is removed from the hot end. KilnSimu allows for flexible modeling of feed and gas flows, where there can be multiple feed positions along the kiln, with at least one bed feed at the feed end and one gas feed at the burner end. This mode is commonly used in most industrial kilns.
Co-current mode
In co-current mode, both the feed material and the hot gas enter the kiln from the same end and move in the same direction. The material is heated by the gases as they flow together towards the exit, and the final product is removed at the hot end. KilnSimu supports co-current flow setups, where the gas flow direction is reversed compared to counter-current mode, and the burner end and feed end coincide. This mode is less common but can be beneficial in certain processes requiring specific heat transfer dynamics.
BED MOVEMENT TYPES
Kiln bed dynamics: accurately simulate material flow
KilnSimu allows for accurate modeling of different types of material flow within the kiln. Depending on factors such as bed properties and kiln rotation speed, users can simulate sliding, slumping, or rolling bed movements. This capability helps to understand material behavior and to optimize kiln design and operation for maximum efficiency.
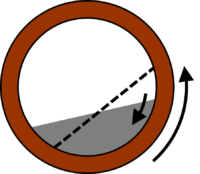
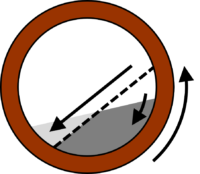
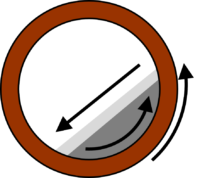
HEAT TRANSFER MECHANISMS
Thermal behavior: simulate and optimize heat transfer
KilnSimu supports both direct and indirect heating mechanisms, providing a comprehensive approach to simulating heat transfer.
The model accounts for convection from the gas to surfaces, such as the kiln wall or the bed surface. Conduction is also modeled, capturing heat transfer between the wall and bed surfaces in contact. Additionally, KilnSimu includes radial radiation, including interactions between the kiln wall, the bed surface, and the gas, all of which are treated as gray bodies. This ensures a thorough understanding of thermal profiles, enabling users to minimize energy loss and improve process performance.
Although electrically heated furnaces were not originally included in the design of KilnSimu, a workaround has been implemented to accommodate this heating method.
TRAINING & SUPPORT
Comprehensive support for your KilnSimu journey
To ensure you get the most out of KilnSimu, each license includes an initial training session designed to familiarize you with the software setup, core functionality, and best practices for effective use. This training serves as a solid foundation for understanding the capabilities of KilnSimu and ensures that you are well-equipped to begin modeling and optimizing your rotary kiln processes.
KilnSimu’s advanced kiln simulation features comprehensive training and support
In addition to the initial session, we provide ongoing support for general inquiries to help you resolve minor questions or technical issues. For more complex challenges, we offer consulting services tailored to your specific needs. Whether you’re exploring new modeling possibilities or optimizing your existing processes, our team is available to guide you through the process with professional expertise.